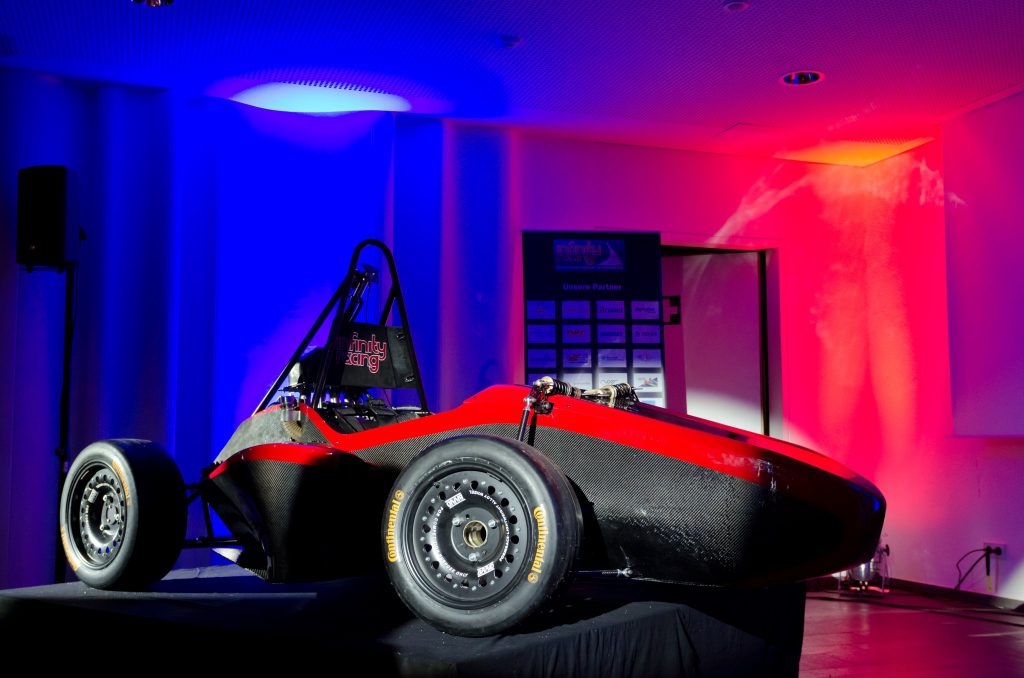
Allgemeines
- Leistung: 63 kW/ 85 PS, max. 10.000 U/min
- Drehmoment: 62 Nm, max. 9.000 U/min
- Gewicht: 220 kg
- Beschleunigung 0 – 100 km/h: 3,8
- Eventteilnahmen: Formula Student Germany, Formula Student Spain, Formula Student Italy
Antrieb
- Kettentrieb
- Drexler Lamellensperrdifferential
- Elektropneumatisch betätigtes Getriebe (4 – Gang)
Für die Primärübersetzung setzten wir beim TOMSOI IV erneut auf das Original-6-Gang-Getriebe der Yamaha R6, jedoch stellten wir beim diesjährigen Auto wieder auf eine pneumatische Betätigung mit einer besonders leichten Hochdruckflasche als Energiespeicher um. Die Pneumatik hat den entscheidenden Vorteil eine komplett separate Energiequelle zu sein. So wird keine elektrische Energie benötigt, die wiederum Motorleistung kostet. Ein Hochschalten ohne Zugkraftunterbrechung ist erneut über eine Variante mit Zündunterbrechung realisiert worden, bei der wir die Schaltzeiten nochmals optimierten. Eine Neuerung des diesjährigen Fahrzeugs ist das Herunterschalten des Getriebes ohne manuelle Kupplungsbetätigung durch den Fahrer, dabei öffnet ein weiterer Pneumatikzylinder automatisch die Kupplung und schließt sie nach dem Gangwechsel wieder. Die Schaltimpulse für die Gangwechsel lösen wir erneut über zwei integrierte Schaltwippen im Lenkrad aus.
Der Sekundärantrieb wird weiterhin mit einer reibungsoptimierten Kette ausgeführt, bei der wir die Kettenspannung über zwei exzentrische Lagerungen des Kettenrades in den beiden Differentialhaltern realisiert haben. Die Übersetzung des Sekundärantriebs wurde nochmals kürzer gewählt, um die Beschleunigung des Fahrzeuges zu verbessern und die Drehzahlsprünge zwischen den einzelnen Schaltstufen zu verkürzen. Dadurch arbeitet der Motor noch länger in einem effektiven Drehzahlbereich. Beim Differential fiel die Entscheidung erneut auf ein speziell für die Formula Student entwickeltes Sperrdifferential der Firma Drexler Motorsport. Durch ausgiebige Lastfall-Analysen und darauf aufbauenden FEM-Berechnungen konnte das Gewicht an den Differentialhaltern, den Exzentern und den zugehörigen Kugellagern um insgesamt 42,3% gesenkt werden.
Um die Längenänderung der Antriebswellen beim Ein- und Ausfedern des Fahrwerks auszugleichen, nutzten wir erneut Tripoden-Gleichlaufgelenke. Da die Antriebswellen zu den rotierenden und teils ungefederten Massen gehören, suchten wir nach noch leichteren Alternativen. Hierbei fanden wir bei RCV-Performance hohle Antriebswellen, die ebenfalls speziell für Formula-Student-Teams angefertigt werden.
Chassis
- Stahl- Gitterrohrrahmen
- Karosserie aus kohlefaserverstärktem Kunststoff, Infiltrationsverfahren
Bei unserem vierten Rennboliden, dem TOMSOI IV, wurde erneut das bewährte Konzept eines Stahl-Gitterrohrrahmens verwendet, dessen Gesamtgewicht mit allen angebrachten Haltern ca. 33kg beträgt. Um eine sichere und stabile Einleitung der Fahrwerkskräfte in den Rahmen zu gewährleisten, wurden wiederum die Knotenpunkte auf die Aufnahmepunkte des Fahrwerks gesetzt. Eine Neuerung des Rahmens des TOMSOI IV ist der Wegfall des komplexen Rahmenabschnittes hinter dem Motor. Dies wurde durch ein äußerst kompaktes Package und eine komplett neue Fahrwerkskinematik der Hinterachse ermöglicht. Durch die Einsparung des Hinterwagens konnte die Gewichtseinsparung sowie die Wartungsfreundlichkeit des Fahrzeuges äußerst gesteigert werden.
Die zentralen Elemente des Gitterrohrrahmens sind die beiden reglementierten Überrollbügen, der Front Hoop und der Main Hoop. Diese konnten mit einer CNC-Biegemaschine genau nach unseren Wünschen gebogen werden. Durch die letztjährig gesammelten Erfahrungen mit zugeschnittenen Rohren, konnten wir dieses Jahr die Rohrverschneidungen der einzelnen Rohre noch detaillierter ausführen. Durch diese beiden Aspekte, dem erstmals eingesetzten 3D-Schweißtisch und der speziell dafür angefertigten Rahmenlehren, konnte die Genauigkeit des Gitterrohrrahmens enorm gesteigert werden. Dadurch verbesserte sich die Passgenauigkeit der vorbereiteten Halter für das Fahrwerk und sonstige Komponenten des Fahrzeuges deutlich und die weitere Fertigung des Rahmens wurde entscheidend vereinfacht.
Durch die noch detailliertere Berechnung des Rahmens mit Hilfe der „Finite Elemente Methode“, konnte die Torsionssteifigkeit noch genauer bestimmt werden. Die Verwendung der sogenannten Balkenmethoden verhalf, dank schnell durchführbaren Änderungen am Rahmen und der geringen Berechnungszeit, zu zahlreichen und schnellen Berechnungen verschiedener Varianten des Gitterrohrrahmens. So konnte die Torsionssteifigkeit des Rahmens durch ein minimales Mehrgewicht auf einen Wert von 2300 Nm/Grad gesteigert werden.
Elektronik & Informatik
- uC-Getriebesteuerung mit CAN-Interface
- LCD-Dashboard
- Bosch Motorsport C50 Datenlogger
- 868MHz SRD-Band Telemetrie
Erneut griffen wir während der Planungsphase des TOMSOI IV auf das bewährte Konzept verschiedener ECUs mit überschaubarer Funktionalität zurück. Ziel war es abermals, voneinander unabhängige und eigenständige Steuergeräte zu entwickeln. Die hervorragende technische Dokumentation sowie der gute Support während der Hard- und Softwareentwicklung waren ausschlaggebende Argumente, den bewährten ATMEL AT90CAN128 als Mikrocontroller zu wählen.
Ziel der Hardwareentwicklung war es in erster Linie, die bestehenden Module (Getriebesteuerung und Live-Telemetrie) kompakter zu designen um somit den benötigten Platzbedarf zu minimieren.
Das Display mit integriertem Datenlogger findet im Cockpit des TOMSOI IV keinen Platz mehr, als Ersatz der DDU Sport kommt eine Eigenentwicklung mit zwei LC-Displays und einer 7-Segment-Anzeige zum Einsatz.
Ein Datenlogger der neuesten Generation von Bosch Motorsport mit u.a. zwei frei programmierbaren CAN-Interfaces sowie 6 Analogeingängen zeichnet sämtliche Parameter des Motor- und ABS-Steuergeräts auf. Federwegaufnehmer, Lenkwinkelsensor und weitere Messdaten werden über die Analog- und Digitaleingänge erfasst.
Zur Fahrzeugüberwachung am Streckenrand kommt eine kompaktere Version des letztjährigen Telemetriemoduls zum Einsatz. Erneut werden sämtliche Parameter im ISM-Band mit der Frequenz 868 MHz übertragen. Eine erweiterte und angepasste Visualisierungssoftware soll das auswerten nochmals erleichtern.
Bedingt durch die realisierte pneumatische Betätigung der Gangschaltung, reduzierten sich die nun erforderlichen Schaltleistungen der Getriebesteuerung erheblich. Resultierend konnten wir die Bauteile kleiner dimensionieren und die Leiterplattenfläche gegenüber dem Vorjahr um die Hälfte verkleinern, bei gleichzeitig steigender Funktionalität. Die Getriebesteuerung erfasst die Getriebedrehzahl zur Kontrolle der Schaltvorgänge sowie der Berechnung des aktuellen Gangs. Die Fahrer werden zusätzlich durch automatisiertes betätigen der Kupplung beim herunterschalten entlastet.
Wie im Motorsport üblich kommen ausschließlich Hochleistungsmaterialien aus dem Luftfahrtbereich bei der Kabelbaumfertigung zum Einsatz. Spec55 Kabel und DR-25 Schrumfpschläuche entsprechen den Anforderungen, auch unter hohen Temperaturen und dem Kontakt zu Chemikalien wie Kraftstoff oder Bremsflüssigkeit eine fehlerfreie Signalübertragung sowie die Spannungsversorgung sicherzustellen. Kurze Kabelwege und kleinstmögliche Leitungsquerschnitte halten das Gesamtgewicht auf einem sehr niedrigen Niveau. Eine LiFePO4 Batterie mit 6,9Ah wurde wegen der hohen Energiedichte bei gleichzeitig sehr niedrigem Gewicht ausgewählt.
Fahrwerk
- Doppelte, ungleichlange Dreiecksquerlenker in Aluminium-CFK
Hybridbauweise - Vorne und hinten über Pushrods betätigte Penske
Federdämpfereinheit - Radstand: 1650mm
- Spurbreite: vorne/hinten 1200/1150
- Bremsen: vorne 4 Kolben, hinten 2 Kolben Bremszangen
- Bosch Rennsport ABS M4
Konzept und Kinematik
Bei der Konzipierung des Fahrwerks für den TOMSOI IV wurde erneut eine Konstruktion bestehend aus Doppelquerlenkern und einer Druckstab-Betätigung der Feder/Stoßdämpfer-Einheit sowohl an der Vorder- als auch an der Hinterachse eingesetzt. Die Ausführung von Querlenkern, Spurstangen und Druckstäben konnten wie bereits beim Vorgängermodell in einer CFK/Aluminium-Hybrid-Bauweise realisiert werden. Im Vergleich zum letztjährigen Fahrzeug wurde der Radstand um 100mm verkürzt und beträgt nun 1550mm. Ebenfalls wurde eine Verschmälerung der Spurweiten des Fahrzeuges auf 1200mm an der Vorderachse und 1150mm an der Hinterachse durchgeführt. Durch den kürzeren Radstand und die schmälere Spurweite ließ sich die Handlichkeit des Fahrzeuges enorm steigern. Um das Potential der Slick-Reifen optimal ausnutzen zu können, wurde die Fahrwerkskinematik nochmals weiterentwickelt. Anhand der Reifendaten ließen sich die Werte für Sturz und Spur noch besser an den Reifen anpassen. Mit dem erneuten Einsatz eines Rennsport-ABS-Systems ist eine sichere Beherrschung des Fahrzeuges selbst bei widrigen Bedingungen gewährleistet.
Mittels des Fahrwerks-Simulations-Programmes OptimumK wurde die Fahrwerkskinematik ausgelegt und durch die Ausgabe sämtlicher relevanten Daten über das Verhalten des Fahrwerks die Kinematik perfektioniert. Ein besonderes Augenmerk bei der Auslegung wurde auf den Sturzgewinn der Vorderachse beim Einlenken und die gleichmäßige Übersetzung der Dämpferumlenkhebel über den gesamten Federweg gelegt. Aus dem Simulations-Programm konnten die Fahrwerkspunkte an die CAD-Software ProEngineer übertragen werden. Diese Punkte bildeten anschließend im CAD das Skelett für die Konstruktion des Rahmens.
Konstruktion
Anhand der an das CAD-System übertragenen Fahrwerkskinematik konnten nun die einzelnen Baugruppen und -teile auskonstruiert werden. Begonnen wurde mit der Konstruktion der kompletten Querlenker inklusive der Zusammenführungen. Die Querschnitte der verwendeten Carbonrohre wurden beim diesjährigen Boliden weiter optimiert und somit das Gewicht deutlich reduziert. Die Wahl der Felgen fiel erneut auf die besonders leichte Variante des spanischen Herstellers Braid.
Bei der Konstruktion der Radträger und der Radnaben wurde vermehrt auf den Einsatz der „Finite Elemente Methode“ gesetzt um das Gewicht der Bauteile, bei gleichzeitiger Erhöhung der Steifigkeit, zu senken. Die hintere Radnabe wurde erstmals in einer Hybrid-Bauweise aus hochfestem Aluminium und einem Stahl-Insert als Tripodenlaufbahn realisiert. Dadurch konnte das Gewicht der Radbaugruppen um 20% gesenkt werden. Die Gewichtseinsparung bei Querlenkern und Radbaugruppen kommen dem Handling des Rennwagens erheblich zugute, da es sich dabei um ungefederte Massen handelt.
Erstmals wurden Stoßdämpfer des amerikanischen Herstellers Penske eingesetzt. Diese zeichnen sich durch ihre besonders leichte Bauweise bei vollständig einstellbarer Zug- und Druckstufe aus. Die Anordnung der vorderen Stoßdämpfer wurde vom letzten Jahr übernommen, da sich die gegenseitige Abstützung bewährt hat. Durch den einfacheren Aufbau des hinteren Teils des Rahmens musste eine neue Anordnung für die Stoßdämpfer der Hinterachse entworfen werden.
Die Entscheidung für die direkte Anbindung an die vordere Motoraufhängung hatte einen simplen Grund: Sie leitet die auftretenden Kräfte in den stabilen Motorblock ein, somit wird der Rahmen entlastet.
Zur Auslegung des Bremssystems wurde mit den gegebenen Daten des Fahrzeuges (Gewicht, Radstand, Spurweite und Position des Schwerpunktes) die optimale Bremskraftverteilung bestimmt. Daran orientierten sich die Auswahl der Bremssättel und die Dimensionierung der Bremsscheiben. Die Wahl fiel auf 4-Kolben-Sättel an der Vorderachse, auf 2-Kolben-Sättel an der Hinterachse und der Außendurchmesser der Bremsscheiben wurde rundum auf eine Größe von 200mm dimensioniert. Eine Neuerung des TOMSOI IV ist die Verwendung von schwimmenden Bremsscheiben, bei denen sich die Bremsscheibe radial und axial leicht zur Radnabe verschieben kann. Diese Bauweise kompensiert die unterschiedlichen Ausdehnungen von Aluminium-Radnabe und Stahl-Bremsscheibe bei Erwärmung.
Karosserie
Design und Modellierung
Den Anfang bei der Auslegung und Gestaltung unserer Karosserie machten einige Abwägungen der Stärken sowie der vorhandenen Defizite der Außenhaut des TOMSOI III.
Das Ergebnis dieser Überlegungen war die Festlegung, dass für unseren TOMSOI IV sowohl eine bessere Zugänglichkeit an die Bauteile im Fahrzeug, als auch eine Gewichtsreduzierung aller Carbonteile und eine bessere Anpassung an den Rahmen erforderlich sind.
Aus diesem Grund war das Ziel, die Frontpartie (Haube und Nase) nicht wie im Vorjahr aus zwei separaten Teilen zu fertigen, sondern als eine Baugruppe zusammenzulegen. Dies war besonders beim Scrutineering – der technischen Abnahme auf den Events – von Vorteil, da durch die Abnahme eines Karosserieteiles, ohne lange Demontage, der gesamte Fußraum und die Crashbox sichtbar wurden. Auch der Unterboden sollte mit Hilfe eines anderen Laminierverfahrens gewichtstechnisch leichter werden und die Luftführung zum Kühler hin verbessern.
Der nächste Schritt war die Modellierung und Designgebung. Hierfür wurde, wie auch schon beim TOMSOI III, ein 3D-Computergraphik- und Animationsprogramm verwendet. Dieses ermöglicht spezifische Baugruppen wie Rahmen, Crashbox und Querlenker einzufügen und daran angepasst die Karosserie darüber zu ziehen.
Inspiriert von der Formel-1 ergab sich eine schlank wirkende Silhouette mit markanter Haube und Formel-1 typischen Luftöffnungen in den Seitenkästen, welche sich außerdem in geschwungener Form nach hinten verengen. Das schlanke Aussehen wurde vor allem durch die direkt am Rahmen anliegende Karosserie erzielt, wodurch keine übermäßigen Lücken entstanden. Dadurch konnte das Gesamtbild erheblich verbessert werden.
Fertigung
Nachdem die Konstruktion der Außenhaut beendet war, gingen die CAD-Daten der einzelnen Karosserieteile direkt weiter an unseren Sponsor „Kessler Modellbau“, der uns bereits beim
TOMSOI III bei der Fertigung der Laminierformen unterstützte.
Unsere Karosserie unterteilt sich in:
- Zwei Seitenflanken
- Zwei Seitenkasten
- Haube
- Unterboden
Nach den Laminierarbeiten, die direkt bei uns an der Hochschule vorgenommen wurden, bestand der letzte Schritt noch darin, die einzelnen Bauteile an den Rahmen anzupassen, Ausschnitte für Querlenker und sonstige Anbauteile einzufügen und alles am Fahrzeug zu fixieren.
Motor
- Yamaha R6 DOHC Reihenvierzylinder RJ05
- Hubraum: 600 ccm
- Motorsteuerung: Bosch MS 4 Sport
Auch in der nunmehr vierten Auflage unseres TOMSOI-Rennboliden kommt ein aus der Yamaha R6 stammender 600ccm Reihenvierzylindermotor zum Einsatz. Besonders seine Zuverlässigkeit und das Leistungspotential sind Eigenschaften, die für dieses Aggregat sprechen und genau zu unserem Konzept passen.
Mindestens genauso wichtig wie der Motor selber sind die Auswahl und Auslegung seiner Peripherie-Systeme wie z.B. Ansaug-, Abgas- oder Kühlsystem: Aufgrund des besonderen Regelwerks der Formula Student ist es nämlich entweder nicht erlaubt oder nicht sinnvoll, serienmäßige oder für andere Rennserien entwickelte „Fertiglösungen“ zu verwenden.
Besonderes Augenmerk haben wir bei der Entwicklung dieser Systeme auf die Steigerung der Zuverlässigkeit bei gleichzeitiger Gewichtsreduzierung gelegt.
So haben wir im Ansaugsystem beispielsweise die Drosselklappe, die bereits im Vorjahr zum Einsatz kam, durch eine Axialsicherung der Drosselwelle noch betriebssicherer gestaltet, indem so ein Verschieben der Welle und ein dadurch verursachtes Fressen von Drosselklappe und Gehäuse verhindert wird.
Als Beispiel für unser Bestreben nach immer weiter perfektioniertem Leichtbau können in diesem Bereich die Einspritzventil-Adapter aufgeführt werden. Diese Komponente, die die Schnittstelle von Ansaugtrakt und Kraftstoffsystem darstellt, sitzt direkt auf den Einlasskanälen des Motorgehäuses und ist damit gleichzeitig Befestigungspunkt für das Ansaugsystem, die Einspritzventile sowie der Kraftstoffrail, die die Ventile mit unter Druck stehendem Benzin versorgt. Natürlich müssen die Einspritzventil-Adapter allerhöchsten Sicherheitsanforderungen u.a. bezüglich Dauerfestigkeit erfüllen, da bei deren Versagen sehr schnell eine Gefahr, durch Kombination von heißen Motorteilen und unter Druck stehendem Benzin, nicht nur für den Rennwagen, sondern auch für Fahrer und Streckenposten entstehen kann. Dennoch haben wir es geschafft, an diesem Bauteil über 50% Gewicht gegenüber der Vorjahresversion einzusparen bei gleichzeitiger Erhöhung der Sicherheitsfaktoren.
Bei der Schmierölversorgung des Motors haben wir uns wieder für die bewährte Technik des Nasssumpfes entschieden. Diese Lösung bietet gegenüber dem Trockensumpf deutliche Gewichtsvorteile und ist außerdem betriebssicherer, da keine zusätzlichen Pumpen oder Verschlauchungen notwendig sind, die ausfallen oder durch Leckagen zum Ausfall führen können. Natürlich haben wir auch hier einige Details zum Vorgänger verbessert: So ist die aktuelle Ölwanne durch verringerte Wandstärken deutlich leichter geworden. Um eine permanente Ölversorgung zu gewährleisten und das Ansaugen von Luft zu verhindern, wurden Schwallbleche direkt in das Design der Ölwanne integriert. Diese haben nachweislich eine höhere Effizienz als direkt am Ölansaugschnorchel angebrachte Schwallbleche und sind außerdem zuverlässiger als mechanische Klappenventile.
Wie bereits schon erwähnt lagen unsere Ziele in der Steigerung der Zuverlässigkeit und der Gewichtsreduzierung. Im Motorressort haben wir uns zudem als Ziel gesetzt, die Effizienz des Motors weiter zu verbessern. Dies hat neben den offensichtlichen Vorteilen, einem reduzierten Spritverbrauch und damit verbunden eine höhere Platzierung in der Fuel-Efficiency-Wertung, auch noch den entscheidenden Vorteil, dass das Kühlsystem dadurch verkleinert werden kann. So konnte durch ein hohes Engagement bei der Abstimmung des Motors auf dem Prüfstand gleichzeitig ein Gewichtsersparnis am Kühler bewirkt werden. Durch eine gute und enge Zusammenarbeit mit dem Karosserieressort wurden zudemhin der Seitenkasten und der darin liegende Kühlkanal weiter strömungstechnisch optimiert, um eine verbesserte Luftführung durch den Kühler zu realisieren. Außerdem wurde der Kühler näher am Motor und am Fahrzeugschwerpunkt platziert, was zum Einen die Längen der Kühlerverschlauchungen als auch die Massenträgheitsmomente um die Fahrzeughochachse reduziert.
Die größte Innovation –bezogen auf den Motorbereich- hat unser Bolide TOMSOI IV allerdings im Abgassystem erfahren: Hier haben wir das Konzept von Grund auf neu ausgelegt und durch zahlreiche Berechnungen und Simulationen des Gesamtmodells die Krümmerabschnittslängen, -zusammenführungen und –durchmesser an die gewünschte Motorcharakteristik angepasst. Des Weiteren haben wir uns darauf konzentriert, das Abgassystem gewichts- sowie fertigungstechnisch so leicht wie möglich zu gestalten. Dies haben wir durch den Einsatz äußerst dünnwandiger Rohre und dem 3D-CNC-Biegeverfahren realisiert.
Ein weiterer Vorteil des CNC-Biegeverfahrens resultiert aus den längeren Einzelsegmenten, wodurch die Anzahl der Einzelteile und somit wiederum die Anzahl bzw. Längen der Schweißverbindungen verringert wird. Dies führt zu einem reduzierten Ausfallrisiko, da diese Schweißverbindungen im Renneinsatz enormen thermischen und mechanischen Belastungen ausgesetzt werden. Alle Maßnahmen, sowohl konstruktiv als auch auslegungsbedingt, ergaben eine Gewichtseinsparung zum Vorjahr von beachtlichen 4,2 kg!