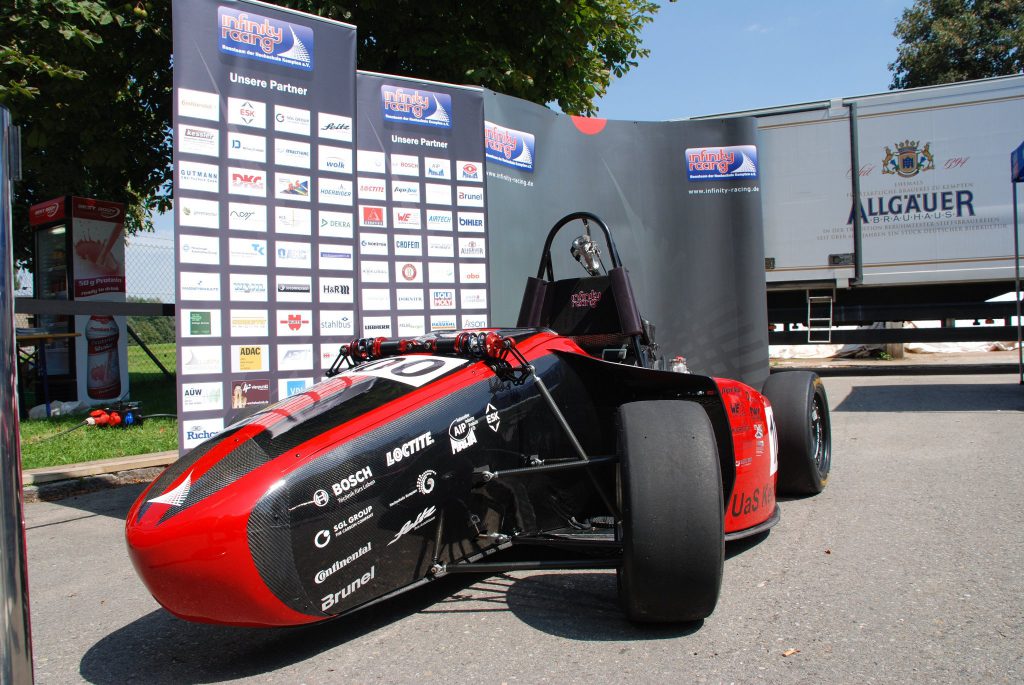
Allgemeines
- Leistung: 63 kW/ 82 PS, max. 10.500 U/min
- Drehmoment: 62 Nm, max. 8.700 U/min
- Gewicht: 250 kg
- Beschleunigung 0 – 100 km/h: 3,8 s
- Eventteilnahmen: Formula Student Germany, Formula Student Italy, Formula Student Spain
Motor
- Yamaha R6 DOHC Reihenvierzylinder RJ05
- Hubraum: 600 ccm
- Motorsteuerung: Bosch MS 4 Sport
Antrieb
- Kettentrieb
- Drexler Lamellensperrdifferential
- Elektromagnetisch betätigtes Getriebe (6 – Gang)
Wie bereits beim vorherigen Fahrzeug, wird auch im TOMSOI III das unveränderte Getriebe des Yamaha R6 Motors für die Primärübersetzung genutzt. Bei der Schaltungsbetätigung erfolgt nun der Umstieg vom pneumatischen zu einem elektromagnetischen Aktuator. Die Betätigung der Schaltung erfolgt hierbei weiterhin über Schaltwippen am Lenkrad.
Die Übersetzung des Kettentriebs wird nun noch kompromissloser in Richtung Beschleunigung, und damit weg von der Höchstgeschwindigkeit, ausgelegt. Dies ergab sich nach ausführlicher Analyse, der bei den Rennen der letzten Saison mit TOMSOI II aufgezeichneten Daten. Von dieser Entscheidung erhoffen wir uns bessere Ergebnisse bei allen dynamischen Prüfungen auf den Wettbewerben, da der Motor nun schon bei niedrigeren Geschwindigkeiten in sein optimales Drehzahlband kommt. Zudem ist die Abstufung der Zugkraft zwischen den einzelnen Gängen harmonischer. Auf Grund der Umbauten, welche reglementbedingt am Motor vorgenommen werden mussten, ist die Abstufung bei Standardübersetzungen, wie sie am Motorrad gefahren werden, nicht mehr so homogen. Dies muss ebenfalls bei der Übersetzungsauslegung bedacht werden.
Beim Differentialgetriebe wird wieder auf die neueste Ausbaustufe von Drexler Motorsport gesetzt.
Um Gewicht zu sparen werden darüber hinaus Hohlwellen der Firma Taylor Racing eingesetzt. Dies fällt insbesondere bei den Antriebswellen ins Gewicht, da es sich hierbei um rotierende, und zur Hälfte ungefederte Masse handelt, welche den Einfluss auf die Fahrdynamik erheblich verstärkt.
Im Gegensatz zum vorherigen Fahrzeug werden nun Tripodegelenke eingesetzt, um somit Federbewegungen des Fahrwerks ausgleichen zu können.
Chassis
- Stahl- Gitterrohrrahmen
- Karosserie aus kohlefaserverstärktem Kunststoff, Infiltrationsverfahren
Das Chassis unseres dritten Boliden ist ein Stahl-Gitterrohrrahmen, bestehend aus einer komplexen Fachwerkstruktur und einem Gewicht von 29 kg. Die Knotenpunkte des Rahmens wurden, wie auch schon bei den letzten beiden Fahrzeugen, an die Aufnahmepunkte des Fahrwerks gesetzt, um die Elastokinematik durch das Chassis zu minimieren. Eine deutliche Gewichtsreduzierung des Rahmens konnte unter anderem dadurch erzielt werden, dass der Motor direkt an den Rahmen geschraubt wird, wodurch sich zusätzliche Motorhalterungen einsparen ließen.
Um die Passgenauigkeit der Schweißarbeiten zu garantieren und qualitativ hochwertige Schweißnähte zu ermöglichen, wurden die einzelnen Rohrabschnitte der Chassistruktur erstmals mittels einer Hochleistungslaserschneidmaschine zugeschnitten. Nahtanhäufungen an Knotenpunkten wurden erstmalig durch den Einsatz von Rohrzwischenstücken verringert. Des Weiteren konnten Gehrungsschnitte durch überstehende Rohrenden vermieden werden. Um eine verbesserte Formgenauigkeit gewährleisten zu können, wurden die sicherheitsrelevanten Überrollbügel, Front Hoop und Main Hoop, mit Hilfe einer hochpräzisen CNC-Biegemaschine gebogen.
Eine weitere Verbesserung der Finiten Element Methode konnte mit Hilfe eines Volumenmodells des Rahmens erzielt werden. Hierbei ist es möglich, im Gegensatz zum Balkenmodell des Vorjahres, weitere bedeutende Fahrzeugkomponenten wie zum Beispiel Motor , Radnabe, Querlenker und Radträger in die Berechnung und Simulation mit aufzunehmen, um so die notwendige Torsionssteifigkeit des Rahmens noch exakter bestimmen zu können.
Elektronik & Informatik
- uC-Getriebesteuerung mit CAN-Interface
- LED-Dotmatrix Ganganzeige
- Bosch DDU Sport Display & Datenlogger
- 868MHz SRD-Band Telemetrie
Nach den Erfahrungen aus der Saison 2009/2010 hat sich das Ressort E&I mehr am KISS-Prinzip orientiert: „Keep it simple and straightforward.“ Um das System „Rennwagen“ einfach und überschaubar zu halten, wird weniger Funktionalität pro Baugruppe integriert und die unabhängige Modulbauweise als eigenständige CAN-Knoten (auf elektrischer und mechanischer Ebene) angestrebt.
Die Neuentwicklung zieht auch einen Wechsel der Mikrocontroller-Basis nach sich. Im Zuge der Recherchen hat sich die 8-Bit Serie megaAVR von ATMEL als gut dokumentiert und technisch ausgereift erwiesen und den Sprung auf die Layouts geschafft.
Das eigenentwickelte TFT-Lenkraddisplay und der Datenlogger fielen dem Rotstift zum Opfer – zunächst Blickfang und Präsentationsobjekt, auf der Kehrseite allerdings Entwicklungszeitfresser und im Rennbetrieb mit wenig effektivem Nutzen, da der Fahrer mit dem sicheren Steuern des Fahrzeugs beschäftigt ist. Die Dashboard-Einheit DDU-Sport von Bosch übernimmt die Funktionalität und stellt gleichzeitig einen 2-Kanal CAN Datenlogger mit 512MB Speicher und analogen Eingängen bereit.
Die Verantwortung zur Überwachung der relevanten Live-Daten wird dem Boxenteam verstärkt übertragen, so soll für den Fahrer eine Informationsentlastung geschaffen werden. Die bewährten 868-MHz Funkmodule werden aus dem Telemetrie-System von TOMSOI II übernommen und die Visualisierungssoftware einer Überarbeitung unterzogen.
Das Embedded System für die elektronische Ansteuerung des Motorrad-Getriebes erfährt in der Saison 2010/2011 ebenfalls starke Änderungen:
Der Wechsel von einer elektropneumatischen- hin zu einer elektromagnetischen Betätigung der Schaltwalze stellt völlig neue Anforderungen an die Stromlieferfähigkeit der Schaltung: Moderne N-Kanal MOSFETS mit RDS(on) von weit unter 10mΩ schalten mit intelligenten High-Side Treibern Ströme von über 10A und sorgen für geringe Schaltverluste vor dem niederohmigen, induktiven Aktuator von Magnet-Schultz.
Ein Workshop zur Kabelbaum-Verarbeitung bei Bosch hat dem Ressort E&I das nötige Wissen vermittelt, die Schutzklasse der elementaren Stromversorgung und Signalverteilung zu erhöhen. Dabei liegt das Augenmerk auf kurzen Verbindungsstrecken und knappen Querschnitten, um das Gesamtgewicht gering zu halten.
Fahrwerk
- Doppelte, ungleichlange Dreiecksquerlenker in Aluminium-CFK
- Hybridbauweise
- Vorne und hinten über Pushrods betätigte Sachs Federdämpfereinheit
- Radstand: 1650mm
- Spurbreite: vorne/hinten 1280/1230
- Bremsen: vorne 4 Kolben, hinten 2 Kolben Bremszangen
- Bosch Rennsport ABS M4
Konzept und Kinematik
Das Fahrwerk unseres TOMSOI III wurde gegenüber dem des TOMSOI II stark modifiziert. Hauptaugenmerk lag hierbei auf einer neuen Kinematik, der Betätigung der Stoßdämpfer über einen Druckstab, einer Realisierung der Querlenker als CFK/Aluminium Hybrid Konstruktion sowie der Integration eines Rennsport ABS.Nachdem das Konzept erst einmal abgesteckt war, musste man sich zunächst intensiv mit den Reifendaten unserer Slicks von Continental beschäftigen, um somit ermitteln zu können, was der Reifen vom Fahrwerk abverlangt. Diese Aufgabe ist besonders wichtig, da die Haftung eines Formula Student Boliden ausschließlich über die Reifen ohne die Unterstützung von Spoilern oder eines Diffusors generiert wird.
Die Kinematik selbst wurde mittels des Programms Optimum K ausgelegt. Diese Software zeichnet sich durch eine intuitive Bedienbarkeit sowie einen leichten Datenaustausch zu unserem CAD System aus. Ziele hierbei waren unter anderem die zum Teil stark migrierenden Rollzentren der alten Kinematik zu unterbinden, das Übersetzungsverhältnis der Umlenkhebel über den gesamten Federweg linear zu halten und die Lenkkräfte durch eine Einführung eines „Nachlaufversatzes“ im Rahmen zu halten.
Im Anschluss daran wurden die gewonnen Punkte aus der Kinematik Software in das CAD-System Pro Engineer Wilfried 4 übertragen und bildeten somit das Skelett des TOMSOIII. In mehreren Durchgängen wurde in Zusammenarbeit mit dem Ressort Rahmen die Kinematik an das Packaging und die Templates angepasst.
Konstruktion
Nachdem der Rahmen und die Kinematik im CAD fix waren, stand als nächstes die Auskonstruktion der einzelnen Baugruppen und Teile auf dem Programm. Begonnen wurde mit der Auswahl einer geeigneten Felge. Dazu wurden mehrere Felgen auf Gewicht und Bauraum untersucht, bis man sich letzten Endes für diejenigen des spanischen Herstellers BRAID entschied. Dies lag zum einen daran, dass die Felgen mit einem Gewicht von nur 3,2 Kilo nun ca. 30% leichter als die des letztjährigen Boliden sind, zum anderen konnte der Hersteller flexibel auf unsere Wünsche bezüglich des Lochkreises und der Einpresstiefe eingehen. Die der in der Felge liegenden Radnabe und Radträger wurde wie beim Vorgänger wieder als eine Konstruktion aus hochfestem Aluminium realisiert. Durch den Einsatz größerer Lager und Topologie-Optimierungen ließ sich das Gewicht um25% senken, während gleichzeitig die Gesamtsteifigkeit der Baugruppe um 30% gesteigert werden konnte.
Die Stoßdämpfer stammen, wie auch bei den letzten beiden Boliden, wieder aus dem Hause SACHS und wurden mit Federn der Firma H&R bestückt. Die größte Änderung besteht in der Positionierung der Stoßdämpfer im Fahrzeug, da diese diesmal mittels eines Druckstabes betätigt werden und so gelegt sind, dass sie sich beim Einfedern gegenseitig abstützen.
Die Querlenker des TOMSOI III werden erstmals als CFK Querlenker ausgeführt. Ziel war die Reduzierung der kritischen ungefederten Masse bei gleichzeitiger Erhöhung der Steifigkeit des Fahrwerks. Bei dieser Hybridkonstruktion wurden in den nach unserem Wünschen gefertigten Kohlefaserrohre Inserts aus hochfestem Aluminium eingeklebt.
Grundlage für die Auslegung des Bremssystems war das vollparametrische Bremskraftverteilungsdiagramm. Mit den daraus gewonnenen Erkenntnissen konnten die Bremszangen und Geberzylinder dimensioniert und ausgewählt werden. Die 4-Kolben-Sättel an der Vorder- und die 2-Kolben-Sättel an der Hinterachse sowie die Geberzylinder stammen von AP Racing. Eine Neuheit und zugleich ein Highlight des TOMSOI III ist die Einführung des Rennsport ABS von Bosch. Dieses System erlaubt dem Fahrer immer mit dem optimalem Reifenschlupf abzubremsen und folglich den geringsten Bremsweg auch bei den verschiedensten Streckenbedingungen zu erhalten.
Karosserie
Die Designfindungs- und Entwicklungsphase der TOMSOI III – Karosserie wurde mit klassischen Handskizzen begonnen, um einen ersten Entwurf der Außenhaut zu gestalten. Nach Absprache hinsichtlich zukünftiger Montagearbeiten wurde die Aufteilung der Karosserie, samt Überlappungs- und Verschraubungsflächen, festgelegt. Auch die Beschnittkanten der einzelnen Karosseriesegmente wurden schon im sehr frühen Stadium des Entwicklungsfortschritts angeordnet. Aufgrund der gründlichen und konsequenten Vorüberlegungen war es uns möglich, ein gewisses Wiedererkennungsmerkmal der TOMSOI II – Karosserie zu übernehmen. Das Erscheinungsbild der schlanken Frontpartie vom Vorjahresfahrzeug wurde in abgeänderter und angepasster Form für unsere neue Außenhaut übernommen. Zwei wesentliche Punkte bei der Gestaltung der neuen Karosserie war zum einen, einen Kühlkanal im linken Seitenkasten zu integrieren um eine optimale Anströmung des Fahrzeugkühlers zu gewährleisten, und zum anderen, die Reduktion des Gesamtgewichts der Karosserie erheblich zu verringern. Vom gänzlich neu ausgelegten Kühlsystem mit integriertem Kühlkanal, der zugleich auch die Funktion eines geschlossenen Seitenkastens und die Luftabführung übernimmt, erhoffen wir uns deutlich verbesserte Fahrleistungen im Rennbetrieb.
Nachdem alle Vorarbeiten gründlich erledigt wurden gingen wir im Anschluss in die Konstruktionsphase über. Für die Flächengenerierung entschieden wir uns hierbei für ein 3D-Computergraphik- und Animationsprogramm, das im Flächendesign ein breites Anwendungsspektrum vorweisen kann.
Das CAD-Package unseres Rennwagens wurde, bezogen auf Front-, Seiten- und Rückansicht sowie Draufsicht, maßstäblich in das Programm eingelesen, um anschließend die Flächen gemäß der gewünschten äußeren Form zu generieren. Die so erzeugten Flächen wurden im Anschluss in ein CAD-Programm übernommen und können für die Weiterverarbeitung im Hinblick auf die Konstruktion und Fräsbearbeitung der Laminierformen verwendet werden.
Insgesamt wird die Karosserie für den TOMSOI III aus sechs unterschiedlichen Segmenten zusammengesetzt:
- Zwei Seitenkästen
- Zwei Seitenwände
- Frontpartie
- Unterboden
Ansaugsystem
Da bei der Formula Student, Reglement bedingt, das originale Ansaugsystem abgeändert und folglich selbst entwickelt werden muss, ändern sich die optimalen Ventilsteuerzeiten und müssen somit an die neuen Bedingungen angepasst werden.
In der Simulation wurde deutlich, dass die Seriennockenwellen ein Rückströmen aus dem Zylinder in das Ansaugsystem beim ausstoßenden Takt zulassen. Das ist u.a. die Auswirkung einer zu großen Ventilüberschneidung (=Aus- und Einlassventile gleichzeitig offen). Zudem schloss das Einlassventil zu spät, daher strömte Gemisch im ansaugenden Takt aus dem Zylinder.
Um die Zylinderfüllung zu optimieren wurde das Profil der Seriennocken geändert und diese auf unsere Bedürfnisse umgeschliffen.
Kühlsystem
Erfahrungen aus der Saison 2009/2010 haben gezeigt, dass im Bereich des Kühlsystems Optimierungspotential besteht. Aus diesem Grund wurden für Tomsoi III diverse Messungen am TOMSOI II Kühlsystem vorgenommen und ausgewertet, intensive Berechnungen und CFD Simulationen unter den Aspekten der An- und Druchströmung, des Wärmeaustauschers und der geometrischen Gestaltung der Luftführung im Seitenkasten, unternommen.