Structure
The chassis allows the driver to utilise the full potential of the vehicle in both longitudinal and lateral directions. Agile and predictable behaviour is the top priority.
- Double wishbone axle in carbon-aluminium composite construction
- Pushrod-actuated spring/damper unit with bell cranks for linear or slightly progressive transmission behaviour
- Top-mounted damper assembly on front and rear axle with interchangeable leaf springs as stabilisers
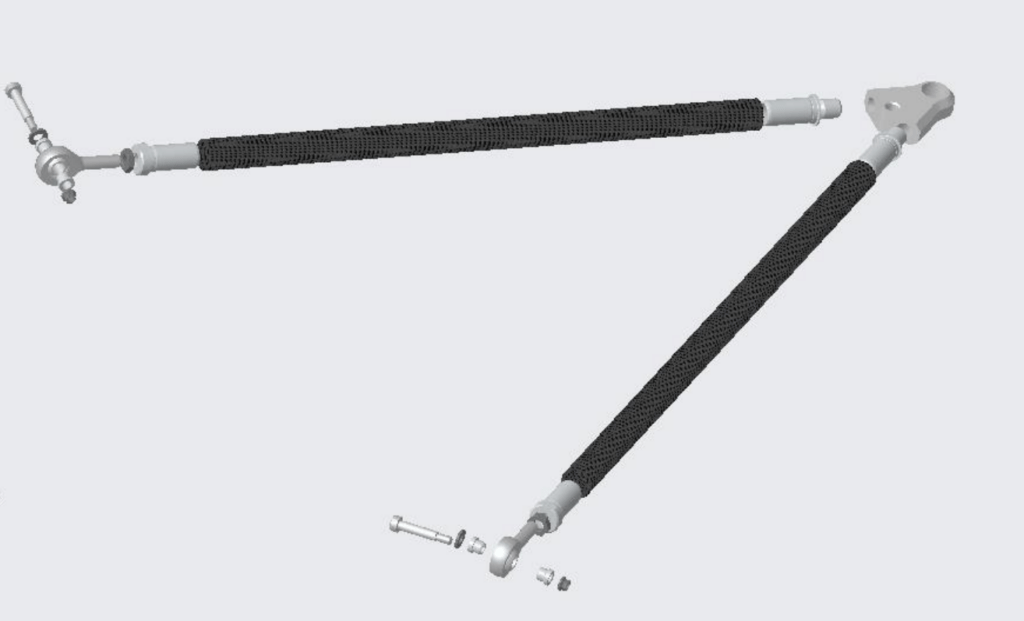
Steering
- Weight-optimised and smooth-running steering gear for low steering forces
- Connection of a steering motor for driverless disciplines directly to the steering gear using a bevel gear
- Separating the bevelled wheels during the disciplines with driver
- Stiff and easy attachment of the handlebar to the monocoque using a bent sheet metal part
Wheel assembly
- Compact and precise wheel carrier for mounting the gearbox and motor
- Customisable and reproducible setup thanks to toe and camber adjustment on the wheel carrier and tie rod
- Powerful 4- or 2-piston brakes on the front and rear axle
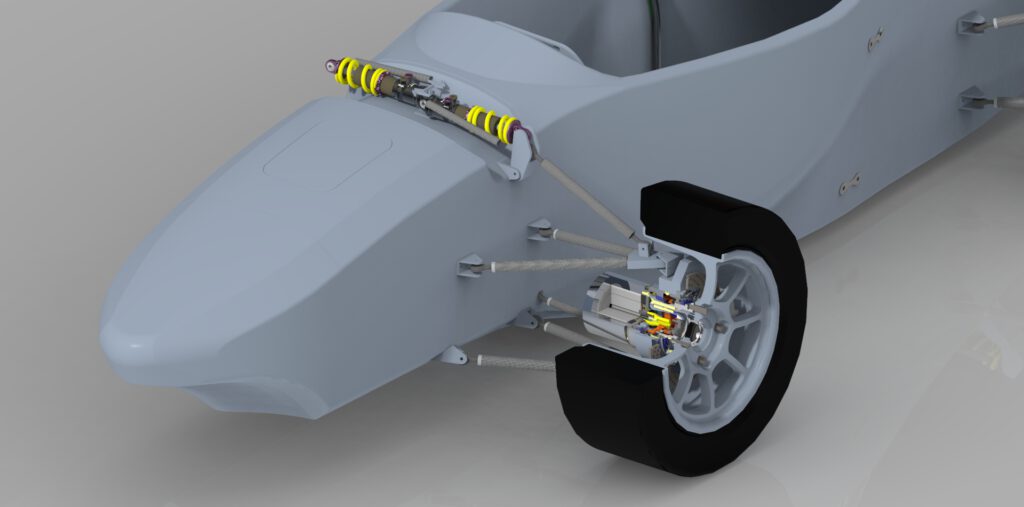
The design of the chassis begins on the asphalt: the top priority is to keep the tyres in contact with the road surface. This means first plotting measured variables from tyre tests and adjusting the kinematics of the wishbones, track rods and bell cranks.
With the different disciplines and competing variables in the kinematics, a balance must always be struck. For example, good steering feedback and directional stability simultaneously entail high steering forces in tight bends. A high camber gain improves the lateral force potential of the tyres, but worsens the behaviour when braking or accelerating.
A chassis is therefore never finished, but always ready for improvement!