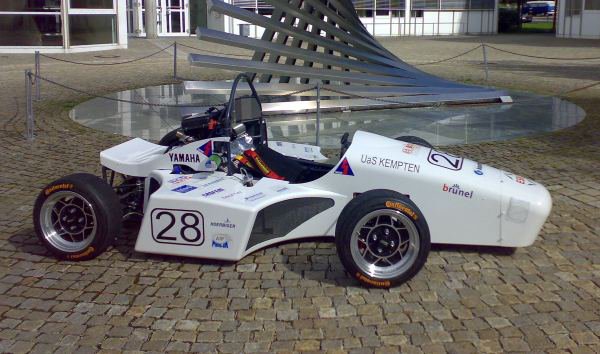
Allgemeines
- Leistung: 61 PS am Getriebeausgang
- Drehmoment: 52 Nm (9000 1/min)
- Gewicht: 332 kg
- Beschleunigung 0 – 100 km/h: 4,8 s
- Eventteilnahmen: Formula Student Germany
Drivetrain
- Kettentrieb
- Quaife Sperrdifferential
- 6-Gang Handschaltung
Die Übertragung des Drehmoments vom Motor auf das Differential erfolgt über eine 520er Kette. Dieses drehmomentfühlende Torsen Sperrdifferential stammt aus dem Haus Quaife und ist direkt am Rahmen abgestützt. Die Kettenspannung wird durch zwei Gewindestangen am Differentialhalter eingestellt. Um die Kraft vom Ausgleichsgetriebe auf die Straße zu bringen, wurden Antriebswellen aus einem Ford Fiesta auf die benötigte Länge zugesägt und anschließend wieder mittels Reibschweißen zusammengefügt. Auch die Radnaben wurden wegen der passenden Verzahnung für die Wellen aus dem Fiesta entnommen.
Die Betätigung des sequentiellen Getriebes erfolgt manuell durch einen ergonomisch geformten Schalthebel aus dem Cockpit.
Chassis
- Stahl-Gitterrohrrahmen
- Karosserie aus glasfaserverstärktem Kunststoff,
Vakuumpressverfahren
Für das Chassis unseres ersten Rennwagens entschieden wir uns für einen Stahl-Gitterrohrrahmen. Mittels eines Mockups, welches wir aus Holz gefertigte hatten, wurde die Ergonomie, sowie die spätere Sitzposition des Fahrers präzise ermittelt. Auf Basis der ermittelten Maße und Positionen von Komponenten wie zum Beispiel Motor, Pedalbox, Sitzschale und Fahrwerksanbindungen wurde ein CAD-Modell des Gitterrohrrahmens erstellt und anschließend durch eine FEM-Simulation berechnet und optimiert. Erste Erfahrungen hinsichtlich der komplizierten Verschneidungen von Rohren an den Knotenpunkten unseres Rahmens wurden mit einem spezialisierten Rohr-Tool gesammelt.
Elektronik & Informatik
- TFT-Lenkdisplay
- LED-Drehzahlanzeige mit Schaltblitz
- Embedded PC Datenlogger (Linux kernel, CF-Speicher)
- GSM Telemetrie
Als Motorsteuergerät für TOMSOI I kam ein Bosch MS4 Sport zum Einsatz. Im Zuge der Umrüstung des Motors wurde der Kabelbaum von Grund auf neu konzipiert und selbst gefertigt. Einige Yamaha-Komponenten wurden mit Bosch-Teilen ersetzt, u.a. Lambdasonde, Drosselklappensensor, Zündbox sowie weitere Temperatur- und Drucksensoren. Diese Maßnahmen waren für die reibungslose Abstimmung MS4 auf den Yamaha-Motor erforderlich.
Den Kern der weiteren Elektronik stellt der Boardcomputer dar. Hierbei wurde ein Kontron JRex PM mit einem 800 MHz Intel Celeron Prozessor und 256 MB Ram verwendet und der Computer direkt an den 1 MBit High-Speed CAN-Bus angeschlossen. Auf diese Weise konnten folgende Funktionen realisiert werden:
– Data-Logging, d.h. Aufzeichnung aller relevanter Messdaten der ECU zur späteren Auswertung am PC
– Echtzeitdatenübertragung ausgewählter Meßdaten an die Box via GSM (hierzu wurde ein separates GSM-Modem verwendet und über RS232 angesteuert)
– Visualisierung wichtiger Fahrzeugdaten auf dem Lenkrad-Display
An Software kam auf dem Boardcomputer ein eigens optimierties Linux-System zum Einsatz. Um die verschiedenen Schnittstellen des Boardcomputers unter Linux anzusprechen, mussten dabei zum Teil bestehende Treiber angepasst oder neu entwickelt werden. Auf dem Linux-System setzte die selbst entwickelte, in C++ programmierte Telemetrie-Software tachsys auf, welche die Funktionen des Data-Loggings, der Echtzeitdatenübertragung und der Ansteuerung des Displays auf dem Multifunktionslenktrad beinhaltete. Die Software konnte über WLan konfiguriert werden, wodurch sich beispielsweise festlegen lässt, welche CAN-Nachrichten aufgezeichnet werden sollen.
Das Gegenstück zu tachsys für den PC bildete der in Java geschriebene Racing Monitor, mit dem die aufgezeichneten Daten grafisch angezeigt werden konnten.
Im Multifunktionslenkrad kam ein tageslichttaugliches Display der Firma Simplify Technologies zum Einsatz. Über einige Taster am Lenkrad war es zudem möglich, zwischen verschiedenen Bildschirmseiten umzuschalten. Die Auswertung dieser Taster erfolgte über ein selbst-gelayoutetes und gefertiges Board auf Basis eines Microchip PIC Controllers, welcher auch die Ansteuerung der LEDs für die Drehzahl und den Schaltblitz im Cockpit übernahm.
Karosserie
Beim Design unseres ersten Formula Student Boliden versetzten wir uns in die goldene Ära des Motorsports der 60er und 70er Jahre des vergangenen Jahrhunderts zurück. Klassische Formen und gerade Linien prägten das Erscheinungsbild der damaligen Formelrennwägen. Aufgrund der klassischen Linienführung war es uns möglich, die Negativformen der Karosseriesegmente ohne die Unterstützung von CNC-gesteuerten Fräszentren herzustellen. Lediglich die Form der Nase und ein Teil der oberen Frontabdeckung wurden aus dem industriellen Modellbau bekannten Kunststoff-Blockmaterial CNC-gefräst. Mittels der CAD-Konstruktion unserer Karosserie leiteten wir sogenannte Spanten-Pläne ab und fertigten die Laminier-Formen aus Pressspanplatten und Kunststoff-Blockmaterial selbst. Handwerkliches Geschick sowie professionelle Vorarbeit im CAD halfen uns bei der raschen Umsetzung des Formenbaus. Mittels des herkömmlichen Handlaminier-Prozesses von Glasfasergewebe mit Polyesterharz entstanden die ersten GFK-Bauteile der Außenhaut. Nach anschließendem Beschneiden und Verschleifen wurden alle Karosseriesegmente samt Seitenkästen an das Chassis unseres ersten Rennwagens TOMSOI I angepasst und mittels Klipsen und Schrauben befestigt. Direkt im Anschluss an die Anpassungsarbeiten wurde unsere Karosserie für die Lackierung vorbereitet und in einem klassischen Weiß lackiert.
Fahrwerk:
- Doppelte, ungleichlange Dreiecksquerlenker
- Vorne und hinten über Pullrods betätigte Sachs Federdämpfereinheit
- Radstand: 1750 mm
- Spurbreite: vorne/ hinten 1370/ 1350
Motor
- Yamaha R6 DOHC Reihenvierzylinder RJ05
- Hubraum: 600 Kubikzentimeter
- Motorsteuerung: Bosch MS4 Sport
Nachdem in der Anfangsphase eine Realisierung des Formula Student Projektes beschlossen wurde, begann man mit der Recherche nach verlässlichen und umfangreichen Daten, der in Frage kommenden Motoren. So wurden beispielsweise alle Motorradhersteller kontaktiert, welche Fahrzeuge in der gesuchten Hubraumklasse bis 600 cm³ auf dem deutschen bzw. europäischen Markt im Angebot hatten. Bei dieser Recherche hatten wir das Glück, dass die „Yamaha Motor Deutschland GmbH“ uns nicht nur sämtliche benötigten Motordaten, sondern sogar ein komplettes Motorrad (Model: YZF R6 RJ05 BJ 2003-2005) anbot. Dieses Angebot nahmen wir dankend an und begannen damit, alle für uns verwendbaren Komponenten der ehemals zu Serviceschulungen eingesetzten R6, auszubauen. Somit hatten wir nicht nur den Motor als Herzstück unseres entstehenden Rennwagens, sondern weitere wichtige Komponenten wie Kühler, Airbox (für Prüfstandsversuche), Abgassystem und Antriebsstrang (letztere für Rollenprüfstandsversuche).
Jetzt konnte mit der Entwicklung eines eigenen reglementkonformen Ansaugsystems begonnen werden. So schreibt das Reglement beispielsweise vor, dass nur eine Drosselklappe verwendet werden darf, die sich vor dem Luftmassenbegrenzer (Restriktor) und der Airbox befinden muss. Hierbei wählte man den Durchmesser der Drossel mit 35mm deutlich größer als den des darauffolgenden Restriktors mit 20mm, um Strömungsverluste und Verwirbelungen der Drosselklappe auszugleichen. Aus Gründen der einfacheren Fertigung wurde die Drossel als eine zweiteilige, verschraubbare Klappe-Wellen-Verbindung konzipiert. Der Bowdenzugmitnehmer, über den die Drosselklappe gesteuert wird, wurde nichtlinear ausgelegt, um die geometrisch bestimmte geringe Flächenänderung bei großen Öffnungswinkeln zu beschleunigen.
Des Weiteren wurde das Volumen der Airbox -mit ihrer Funktion als Luftsammler, von ursprünglich seriennahen 8,9 L auf 5,75 L verkleinert, um eine bessere Agilität, also ein schnelleres Ansprechverhalten beim Öffnen bzw. Schließen der Drosselklappe zu erzielen.
Außerdem wurden die Schwingsaugrohre, welche sich zwischen Airbox und Zylinderkopf befinden, gegenüber der Serie stark verkürzt um das Drehmoment im oberen Drehzahlbereich zu erhöhen.
Nachdem alle Systemkomponenten berechnet, konstruiert und gefertigt waren, wurde das Gesamtsystem unter Verwendung des Motorsteuergerätes „MS4 Sport“ von Bosch auf dem hochschuleigenen Leistungsprüfstand appliziert und getestet.